Corrosion should be removed from magnesium parts with a – Corrosion, the nemesis of magnesium parts, poses significant challenges to their longevity and performance. Understanding the methods to remove corrosion and implement preventive measures is crucial for maintaining the integrity of these components. This article delves into the intricacies of corrosion removal from magnesium parts, exploring both chemical and mechanical approaches, safety considerations, and effective prevention strategies.
From the application of chromate conversion coatings to the utilization of sandblasting techniques, we will uncover the advantages and disadvantages of each method, providing a comprehensive overview of the available options. Moreover, we will delve into the potential hazards associated with corrosion removal and establish essential safety guidelines to minimize risks.
Methods for Removing Corrosion from Magnesium Parts
Corrosion is a common problem for magnesium parts, as the metal is susceptible to oxidation and other forms of degradation. Various methods can be used to remove corrosion from magnesium parts, including both mechanical and chemical methods. Each method has its own advantages and disadvantages, and the best choice will depend on the specific application.
Chemical Methods for Removing Corrosion, Corrosion should be removed from magnesium parts with a
Chemical methods for removing corrosion from magnesium parts involve the use of chemical solutions to dissolve or convert the corrosion products. One common method is chromate conversion coating, which involves applying a chromate solution to the magnesium surface. The chromate solution reacts with the magnesium to form a protective layer of chromium oxide, which helps to prevent further corrosion.
Other chemical methods for removing corrosion from magnesium parts include the use of acid solutions, such as hydrochloric acid or sulfuric acid. Acid solutions can be effective in removing corrosion, but they can also damage the magnesium surface if they are not used properly.
Mechanical Methods for Removing Corrosion
Mechanical methods for removing corrosion from magnesium parts involve the use of abrasive materials to remove the corrosion products. One common method is sandblasting, which involves using a stream of abrasive particles to blast away the corrosion. Sandblasting can be effective in removing corrosion, but it can also damage the magnesium surface if it is not used properly.
Other mechanical methods for removing corrosion from magnesium parts include the use of wire brushing or grinding. Wire brushing can be used to remove light corrosion, while grinding can be used to remove more severe corrosion.
Safety Considerations When Removing Corrosion from Magnesium Parts
It is important to take safety precautions when removing corrosion from magnesium parts, as the process can generate hazardous fumes and dust. Proper ventilation should be used to remove fumes, and personal protective equipment, such as gloves and respirators, should be worn to protect the skin and lungs.
Prevention of Corrosion on Magnesium Parts
The best way to prevent corrosion on magnesium parts is to protect them from exposure to moisture and other corrosive agents. Magnesium parts should be stored in a dry environment and should be coated with a protective coating, such as paint or sealant, to help prevent corrosion.
Quick FAQs: Corrosion Should Be Removed From Magnesium Parts With A
What are the primary causes of corrosion on magnesium parts?
Exposure to moisture, oxygen, and certain chemicals can trigger corrosion on magnesium parts.
Why is it important to remove corrosion from magnesium parts promptly?
Corrosion can compromise the structural integrity and performance of magnesium parts, leading to premature failure.
Are there any specific safety precautions that should be taken when removing corrosion from magnesium parts?
Yes, proper ventilation, personal protective equipment, and adherence to safety guidelines are essential to minimize risks.
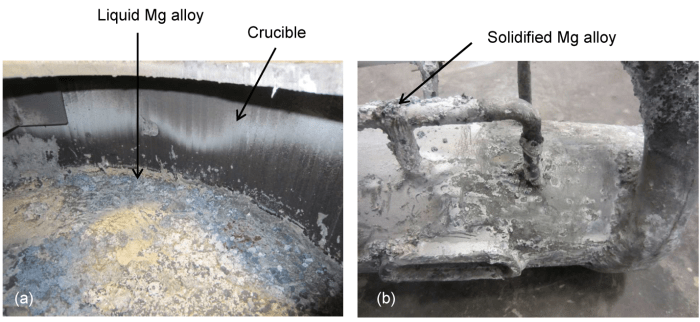
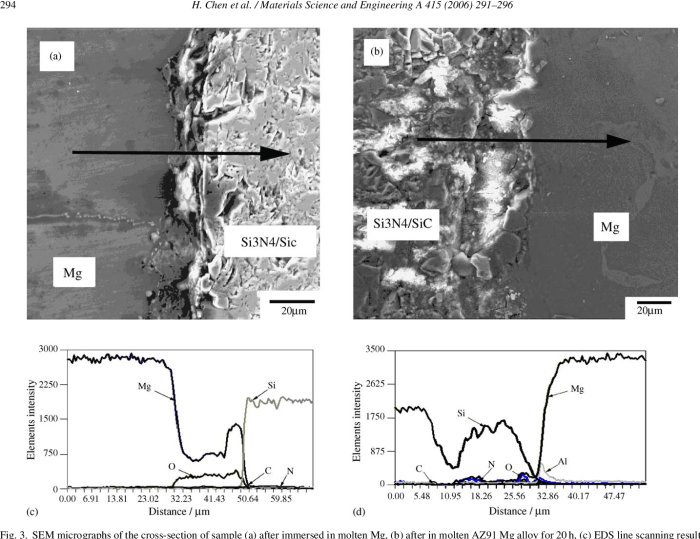